With the latest trend of manufacturing automation promoting the adoption of industry 4.0 "intelligent factory", the need for continuous improvement of visual system becomes crucial. However, in order to promote this ever-increasing level of automation and control, it is also necessary to promote the devices that make these systems work, including image sensors for industrial visual cameras, in order to make this interconnected future possible. For any given device, the scope of these developments will eventually be reflected in the entire data sheet, and the high-level trends involved can be divided into several main areas.
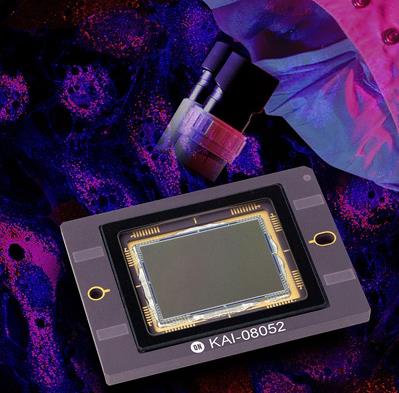
In almost every imaging application, the improved imaging ability is usually closely related to the need to improve the resolution - to provide more pixels to the object to better solve its characteristics. For image sensors, this requirement can be met by reducing the pixel size (achieving higher resolution in a given optical format) or turning to larger devices. However, for industrial imaging, this trend towards higher resolution needs to preserve (or even increase) the frame rate of devices. Therefore, in addition to the higher resolution, the image sensor also needs to provide increased bandwidth - the amount of data per second of the chip, in order to improve the image resolution without slowing down the production line speed. The important point is that with the increasing speed of computer interface (such as USB 3.1, 10gige, etc.), the bandwidth of image sensor does not constitute a data bottleneck in the data flow of the whole system.
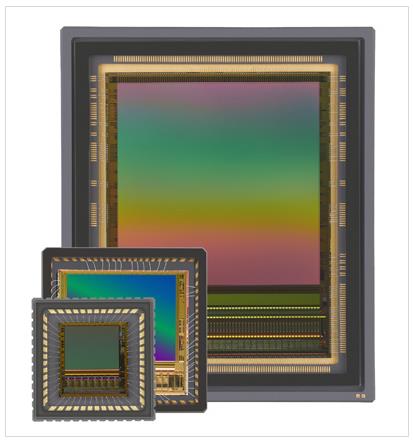
One of the key factors driving the implementation of industry 4.0 is the rise of embedded imaging technology through the deployment of smart cameras throughout the factory floor. However, in order to achieve high efficiency, these embedded cameras must be compact, work with minimum power consumption and low cost - these factors are possible by selecting image sensors for camera design from many aspects. For example, to achieve a compact camera, not only the use of small pixel image sensors, but also the implementation of a complete camera design required to minimize the support circuit architecture. By using low-voltage output for image sensor, power consumption can be reduced, which makes it possible to use low-power devices in the whole camera design process. Moreover, by selecting wisely in image sensor design, cost can be controlled - not only for image sensor, but also for the whole bill of materials of camera.
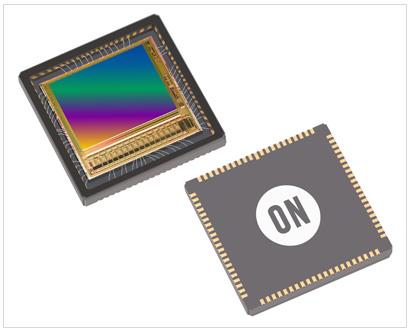
In addition, although some industrial applications need the key image quality and image uniformity that only CCD image sensor can provide at present, many industrial imaging applications usually rely on CMOS image sensor because of its extended feature set (including high data bandwidth). Although the image quality provided by these CMOS devices is enough for many applications, it is still possible to improve the overall image quality, especially in the field of image uniformity by reducing fixed mode noise.
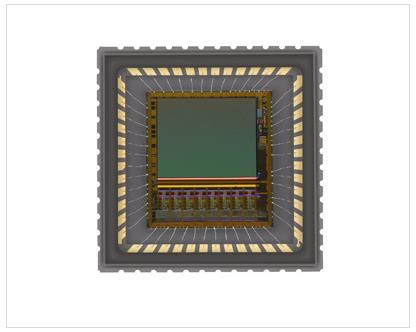
In order to achieve these advances, image sensor suppliers need technologies developed not only for the industrial market, but also for other similar imaging markets. Originally developed for automotive and security imaging, the high dynamic range (HDR) design can be applied to industrial vision to improve imaging in situations where lighting may not be well controlled. The small pixel architecture originally designed for the automotive or consumer electronics market can be adopted directly or expanded to a larger format to provide a larger pixel full well capacity. (this technology can be used in two directions - the global shutter pixel architecture developed for industrial vision can also be used in other similar applications. )In addition, the use of emerging technologies such as 3D TOF, multispectral and hyperspectral imaging will continue to expand to make full use of these technologies as their imaging capabilities are consistent with the larger processing capabilities required. Although all of these image sensor trends - increased bandwidth, more support for embedded vision systems, improved image quality and uniformity, and balanced use of technology - can be categorized as "improved performance," each trend has a separate and significant impact on the continued adoption of industrial vision systems and their expansion to the future "smart factory.". As the level of automation and system intelligence used in manufacturing continues to improve, vision systems - and image sensors that make them work - will continue to play a critical role in the implementation of these technologies.